You will doubtless have heard of HDPE, or high-density polyethylene – an incredibly versatile, useful plastic commonly used in plastic injection moulding. HDPE plastic is made from petroleum and is a thermoplastic polymer. This means that it becomes pliable when heated up and hard again when cool. Its properties allow it to be formed into the required shape very easily and then cooled until it hardens again, via the plastic injection moulding process.
HDPE has a high melting point, which also makes it suitable for the injection moulding process. It was originally created in the 1930s and utilised for short-wave radar cabling during the Second World War.
What’s So Great About HDPE Plastic?
HDPE plastic has many attractive qualities for manufacturers in
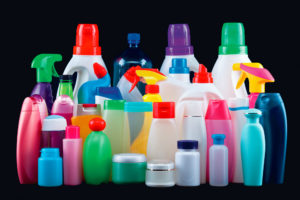
several different sectors. It is light, which means it is great for making cartons and other containers to safely transport contents without adding to the overall weight. Despite this, HDPE plastic is also extremely strong. It is often used in car fuel tanks and other automotive applications, for example, as it is light, but can stand up to the heavy use required due to its strength and durability. Key to many busy households, it is also dishwasher-proof and robust enough to survive prolonged use.
Another advantage to using HDPE plastic is that it offers very good resistance to impacts, chemical damage and other potentially harmful external factors. It can withstand hostile weather conditions too, including UV rays. It can be kept outside or in damp conditions more easily than other materials as it is impervious to water ingress, solvents and many acids and chemicals. HDPE is also safe against mildew, resistant to corrosion and will not rot, rust or succumb to insect damage. HDPE plastic is commonly used to make underground pipes too, for all the reasons above.
HDPE plastics are affordable to produce and will create high-quality, attractive finished goods. The moulded product can be finished in a range of colours and textures, both translucent and opaque and with excellent capacities for printing images, logos and text directly onto the plastic surface or via a label. In some cases, adding colour or pigmentation to HDPE plastic can strengthen the finished product even further.
Adding to that, the lighter weight of HDPE plastic allows it to replace heavier, less environmentally friendly materials in many industrial and other demanding applications. The plastic moulding process uses far less energy than extracting steel from iron ore. So, using HDPE plastic can also help manufacturers contribute to sustainability goals and net-zero carbon targets.
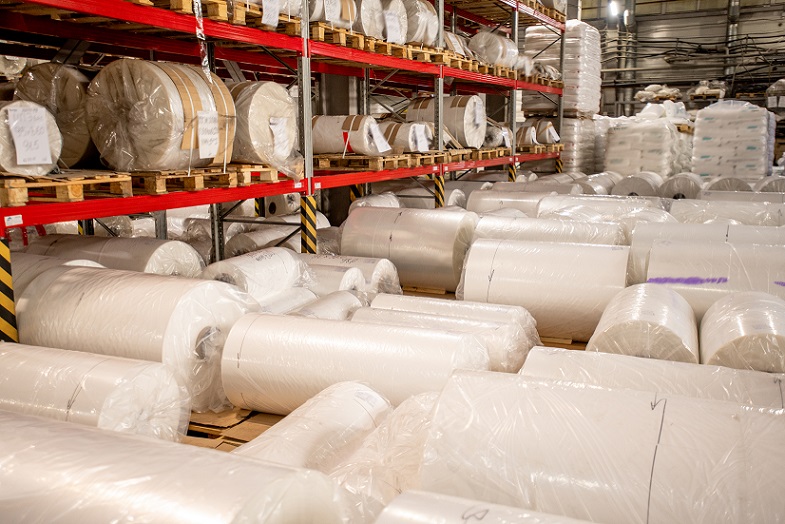
Finally, most HDPE plastic products can be recycled nowadays, lessening their impact on landfills and reducing their carbon footprint. The HDPE plastic can be melted back to a liquid form and reshaped into something else. To check whether a plastic container is made from HDPE and therefore recyclable, check for a symbol with the number ‘2’ inside a triangle of three arrows. This denotes its status as a Type 2 plastic and therefore recyclable. There may also be the letters ‘HDPE’ printed below or near this symbol.
What Else Is HDPE Plastic Used For?
As well to the uses already mentioned above, HDPE plastic has found its way into almost every industry and sector worldwide. Some common applications include:
- Bottles and packaging for detergents, shampoo and soap
- Food and beverage bottles (especially milk and fruit juice), cartons and containers
- Cereal box liners, bread bags and carrier bags for shopping
- Automobile components, fuel tank casings and body parts
- Garden furniture and flower pots
- Toys – both indoor and outdoor
- Shoe lasts
- Filament for 3D printing
- Playground equipment
- Picnic ware
- Cutting boards
- Pipes, cables and insulation
- Outdoor signage
- Promotional materials
- Storage containers and rubbish bins
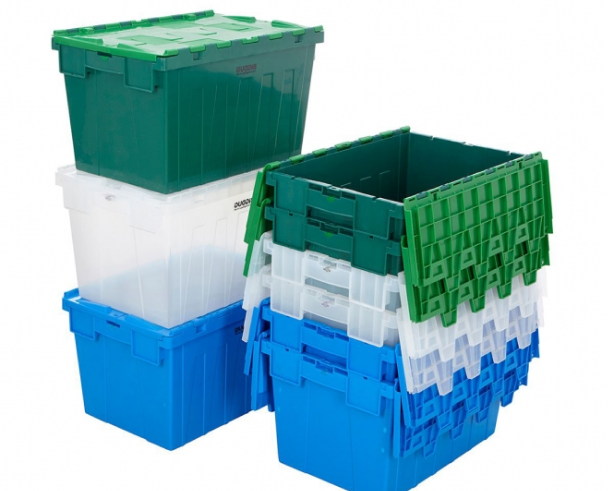
Are there any disadvantages to using HDPE in plastic injection moulding?
As with any plastic or material used in manufacturing, there will be pros and cons to choosing HDPE. Main concerns centre around its sensitivity to cracking and flammability. The material can also be harder to bond than other polymers, so care must be taken to mitigate against this in the injection moulding process. While it can be recycled, HDPE cannot be composted. It also has a less effective temperature capability than other plastics, so it is important to choose the right material for items being exposed to temperature extremes at both ends of the scale.