The defence sector is one where absolute precision and reliance on equipment and machinery is key. Having durable, high-performing equipment can, quite literally, be life-saving. Plastic injection moulding, therefore, is an ideal match for this challenging sector. The components produced are robust, versatile and resistant to weather, chemicals and wear and tear.
Plastic doesn’t conduct heat or electricity, unlike metal, making it a safer choice in some circumstances. The components produced can also be created to highly precise specifications, are easy to clean and maintain and are lightweight for transporting and operating.
Often, it can be very time-consuming to get hold of replacements for equipment or tools that break in the field, so having plastic injection moulded components that can be relied upon to last a long time is also essential. Finally, plastic can be cheaper than other comparable materials, which helps make today’s stretched defence and military budgets go further. Even when more specialist, military-grade specifications and finishes are required.
There are many examples of military grade applications, equipment and components that can be produced using plastic injection moulding techniques for the military and defence sectors. These include:
Communications equipment
Having working communications equipment is vital for most military missions. Personnel must be able to communicate with each other across wide distances and rely on the equipment they are using to get the message across. Components must be accurately manufactured and consistently designed for mass production. There is often a need for rapid manufacturing processes for communications equipment, which is where plastic injection moulding can also offer huge benefits.
Flashlights and scopes
The delicate electronics parts inside equipment such as flashlights and scopes required tough protection. Plastic injection methods can produce durable, robust casings and coverings that are lightweight and effective. Plastic can also be created to be opaque or transparent, making it versatile enough to be used in different parts of the flashlight, including the components protecting the bulb.
Headsets and radios
Again, accurate, reliable and consistent plastic components are crucial in radios and headsets to allow clear, uninterrupted communications to take place. Plastic also provides strong, waterproof coverings for the delicate electronics inside. The plastic injection moulding process enables mass production to be carried out with ease. This is vital for radio equipment, which must be produced in high numbers for distribution across the defence and military sectors.
Helmets and protective gear
It stands to reason that the main property required for helmets and other protective gear is the strength to withstand heavy impacts and the cushioning to protect the head, or body inside from sustaining damage from the impact. There are many plastics that can offer such protection, as well as the ability to be precisely moulded for a close and comfortable fit. The plastic can also be produced in any colour, which is essential when manufacturing items requiring camouflage.
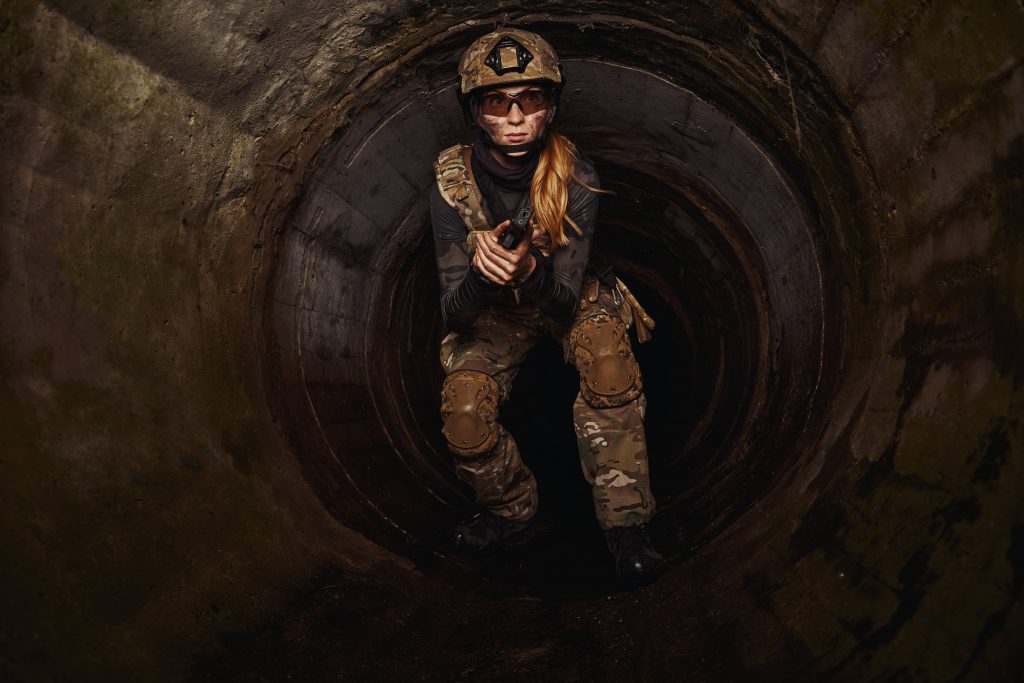
Food canteens and drinks containers
The lightweight, yet robust nature of plastic makes it the perfect material for manufacturing food canteens and water containers. These must often be carried over long distances and the contents must not be contaminated or damaged before they can be consumed. Plastic can also be reused over and over and can be washed and sanitised to a high level of cleanliness.
Kit bag fasteners and hooks
There are countless uses for kit fastenings and hooks in military and defence settings. They hold bags together to prevent the contents from spilling on in transit. They are built for strength to be able to carry large weights and full kit bags. Breakages can waste valuable time and draw attention to soldiers at inopportune times, so they must be durable and tough.
Military vehicle parts
As with the wider automotive industry, more and more vehicle parts are being constructed from plastic now, thanks to its durability, flexibility and the ease of making large quantities of parts that are identical in shape, size and performance. Military vehicles must keep working in extreme conditions and on rough terrain, so durability and high performance are vital for their internal plastic components.
Firearms components
Various polymers are becoming more and more popular in firearms manufacturing due to their lighter weight, enhanced corrosion resistance and lower production costs. The high-precision injection moulding techniques are suitable for several different components, including butt stocks, grips, hand guards, optics, holsters and magazines.