As with any manufacturing process, a finished product can only be as good as its design. Poor design choices in injection moulded components can lead to defects, mismatched components and unattractive finishes. The right design can work wonders, making the parts work as they are supposed to, look amazing and offer excellent scalability, uniformity and strength.
Additionally, the more time and effort that can be put into the design stage, the less time and money will be wasted. After all, creating custom injection moulds can be expensive and using erroneous designs for this stage will have a large impact on costs when they need to be replaced, as well as deadlines when time must be spent correcting things before a single plastic pellet has entered the machine.
Here are five design tips to help you get your plastic injection moulding project right the first time – every time.
Keep it simple
Despite the almost boundless scope for different shapes, sizes and colours, the plastic injection moulding manufacturing method works best when things are kept as simple as possible. Minimum parts, easier shapes and fewer colours will always come out stronger than components with multiple hinges, complicated patterns and awkward angles, corners and sides. If your component must, by its nature, be more complex or perform a more complicated action, spend more time at the beginning to try and simplify things wherever possible. Look at similar designs and see what works and what does not when certain aspects are streamlined or even removed in the name of keeping things straightforward.
Check for uniformity
The designs that result in the best possible flow of molten plastic through the machine and into the mould are those with uniform thicknesses along all of their walls. Keeping walls consistent will prevent the plastic from getting blocked up anywhere, or causing weaknesses where some areas are not covered as well as others. A good rule of thumb for wall thicknesses is to keep the measurements between two and three mm. The standard recommended minimum thickness is one mm, while the thickest ideal for conventional plastic injection moulding methods is four mm.
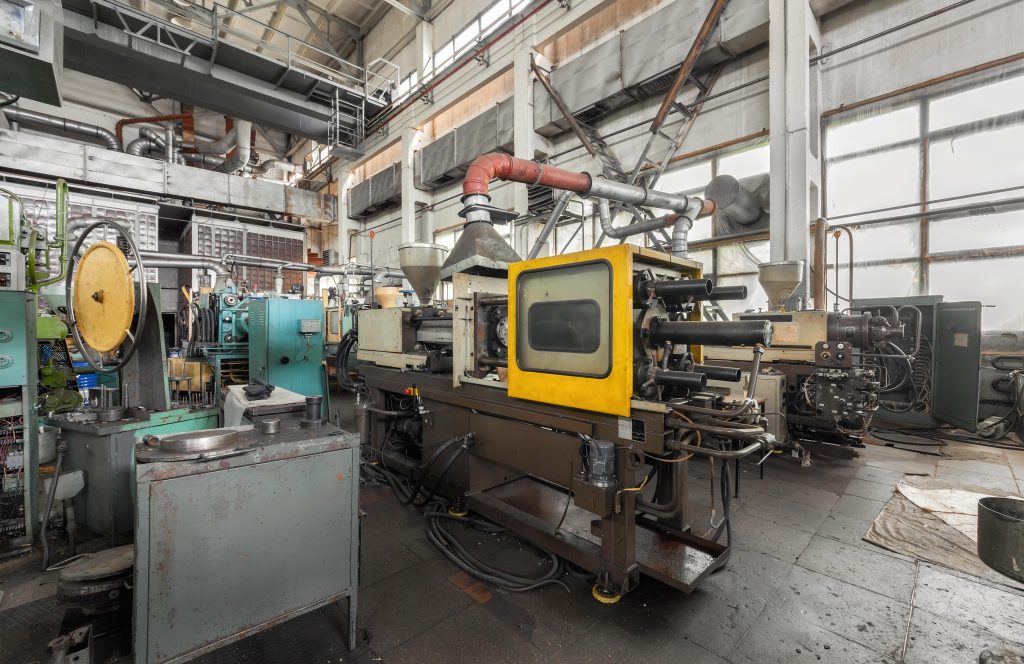
Smooth things out
Again, simplifying matters by avoiding sharp angles and jutting out edges or corners can help strengthen the final component and prevent parts from breaking off once it has been pressed into action. This can also help prevent injury to users through scratching or cutting themselves while operating it. Avoid sharp transitions between wall sections, or in areas where one component will be joined to another. Use radii wherever possible to keep curves and textures smoother. This can also result in a more pleasing aesthetic look for the completed component. Branding, patterns and text can also look nicer printed on smoother surfaces, rather than around sharp angles or on rough finishes.
From thick to thin
The indisputable laws of physics affecting the movement of molten plastic around your newly-designed mould will dictate that moving from thicker areas to thinner ones, instead of the other way round, will ensure a better flow. Starting from the gates inside the injection moulding machine through which the plastic flows, have thicker areas come first. This is so that the plastic can be moved more easily through the mould, won’t clog up at the thinner parts and will get into every crevice and avoid defects. Another thing to watch out for is sink, or local surface depressions where thicker sections cool slower than thinner ones. Ensuring a steady flow can help eliminate this type of defect.
Early and often for prototypes
Design prototypes are a fact of manufacturing, whichever process you opt for. It is something of a false economy to cut out the prototype stage when creating a component. There are so many ways in which a proposed design could go wrong, behave unexpectedly or simply have room for improvement. Good practice for creating and studying prototypes is to introduce them very early on. This stops the design process from going too far down the wrong road, allowing key changes to be made quickly enough to avoid costly mistakes later on. Prototypes should also feature frequently throughout the process, as they guide and inform the efficacy of a design at any stage in its development, not just at the start of the manufacturing project.
Get in touch with Adreco Plastics to discuss your designs and see what we can do for you.